什么是模压成型?
模压成型(又称压制成型或压缩成型)是先将粉状,粒状或纤维状的塑料放入成型温度下的模具型腔中,然后闭模加压而使其成型并固化的作业。模压成型可兼用于热固性塑料,热塑性塑料和橡胶材料。
模压成型工艺是利用树脂固化反应中各阶段特性来实现制品成型的,即模压料塑化、流动并充满模腔,树脂固化。在模压料充满模腔的流动过程中,不仅树脂流动,增强材料也要随之流动,所以模压成型工艺的成型压力较其他工艺方法高,属于高压成型。因此,它既需要能对压力进行控制的液压机,又需要高强度、高精度、耐高温的金属模具。
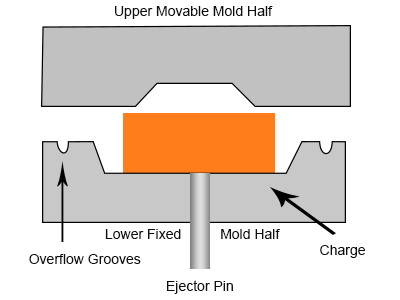
模压成型的应用范围
主要用作结构件、连接件、防护件和电气绝缘件。广泛应用于工业、农业、交通运输、电气、化工、建筑、机械等领域。由于模压制品质量可靠,在兵器、飞机、导弹、卫星上也都得到了应用。
用于模压成型的原材料
通常运用于模压成型制造的材料包括:聚酯玻璃纤维树脂系统 (SMC/BMC/PCM)、聚氨酯蜂窝和纤维复合材料 (PHC)、长纤维增强热塑性塑料 (LFT) 和玻璃纤维毡增强热塑性塑料 (GMT)。
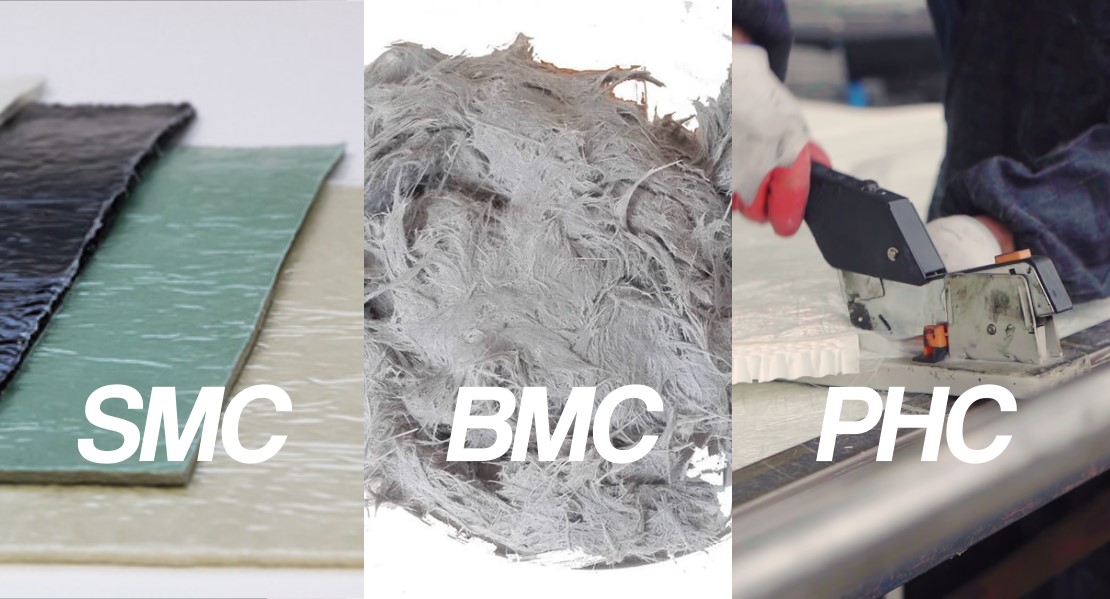
模压成型的特点
大批量程序
短(2-4 分钟)的循环时间和机加工工具钢模具的使用支持每年超过 500,000 个单位的程序量。
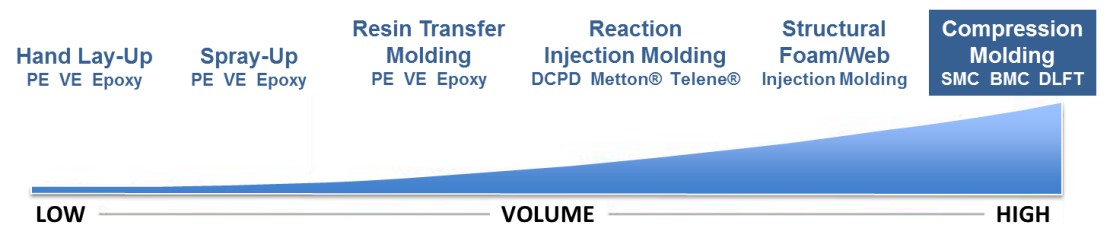
工艺套件中的最佳公差
SMC 配方的高尺寸稳定性和精密匹配模具工具的使用产生了高度稳定和可预测的零件尺寸,进而可以生产出严格公差的组件。
A 级表面
使用可抛光至镜面光洁度的精密匹配模具工具能够实现支持面漆光洁度的汽车级 A 级表面。
广泛的材料特性
通过改变纤维含量、填充材料和性能添加剂,片状模塑料可以获得广泛的材料特性。材料可以针对重量、强度、耐环境性、经济性和许多其他属性进行优化。
模压成型的优点
(1)原料的损失小,不会造成过多的损失(通常为制品质量的2%~5%)。
(2)制品的内应力很低,且翘曲变形也很小,机械性能较稳定。
(3)模腔的磨损很小,模具的维护费用较低。
(4)成型设备的造价较低,其模具结构较简单,制造费用通常比注塑模具或传递成型模具的低。
(5)可成型较大型平板状制品,模压所能成型的制品的尺寸仅由已有的模压机的合模力与模板尺寸所决定。
(6)制品的收缩率小且重复性较好。
(7)可在一给定的模板上放置模腔数量较多的模具,生产率高。
(8)可以适应自动加料与自动取出制品。
(9)生产效率高,便于实现专业化和自动化生产。
(10)产品尺寸精度高,重复性好。
(11)表面光洁,无需二次修饰。
(12)能一次成型结构复杂的制品。
(13)批量生产,价格相对低廉。
模压成型的缺点
(1)整个制作工艺中的成型周期较长,效率低,对工作人员有着较大的体力消耗。
(2)不适合对存在凹陷、侧面斜度或小孔等的复杂制品采用模压成型。
(3)在制作工艺中,要想完全充模存在一定的难度,有一定的技术需求。
(4)在固化阶段结束后,不同的制品有着不同的刚度,对产品性能有所影响。
(5)对有很高尺寸精度要求的制品(尤其对多型腔模具),该工艺有所手短。
(6)最后制品的飞边较厚,而去除飞边的工作量大。
(7)模压成型的不足之处在于模具制造复杂,投资较大,加上受压机限制,最适合于批量生产中小型复合料制品。
模压模具
在设计模压模具时,需要根据产品的尺寸和成型方式来设计型腔,此外,还需要根据产品表面的质量要求和需求选择合适的钢材。模压模具应选用易切削、结构致密、抛光性能好的模具钢。如P20、718、1.273等。另外还要考虑加工精度的相关问题,控制尺寸公差、形状公差和表面粗糙度
为了提高压模表面的耐磨性和耐腐蚀性,通常要进行表面处理。镀铬是最常用的方法之一。镀铬能长期保持金属光泽,在各种酸性介质中稳定,不发生化学反应。镀铬具有优良的耐磨性和高耐热性。当温度达到500℃时,其外观和硬度无明显变化。此外,氮化处理可以大大提高耐磨性。
模压模具的分型线设计应易于脱模,可采用简化顶出机构的方式。产品径向尺寸精度要求较高时,应考虑飞边厚度对m模压产品尺寸精度的影响,垂直分型线可轻松保证产品尺寸精度。
模压模具温度直接影响产品质量和生产效率,温度设计通常在140℃~160℃之间。加热系统包括电加热、蒸汽加热和油加热。在设计模具的温度系统时,选择合适的加热方式,保证模具表面温度均匀,可以减少变形,提高尺寸稳定性。
在设计阶段,使用新的模具软件(CAD/CAM等)掌握压模设计、制造、装配、检验、测试和生产的全过程,包括模具设计和制造成本估算、模具组装评估,模具零件制造工艺评估,模具结构和成型性评估。
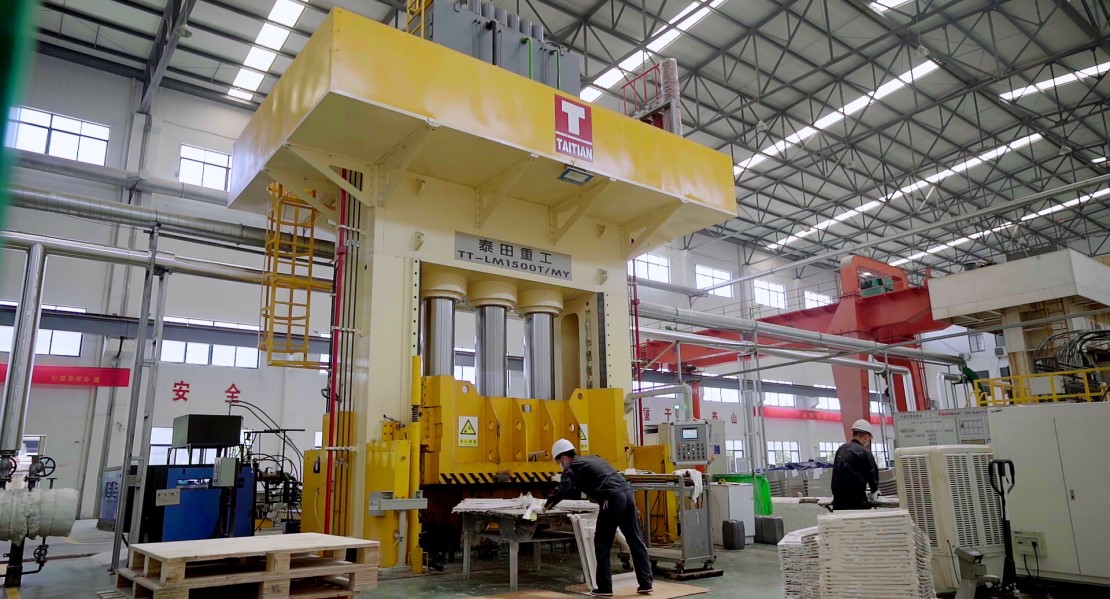